How to Make an F1 Halo
It’s strong enough to support the weight of two African elephants and sturdy enough to deflect a large, full suitcase at a speed of 225kph. So how is motor sport’s new Halo device made to withstand such forces?
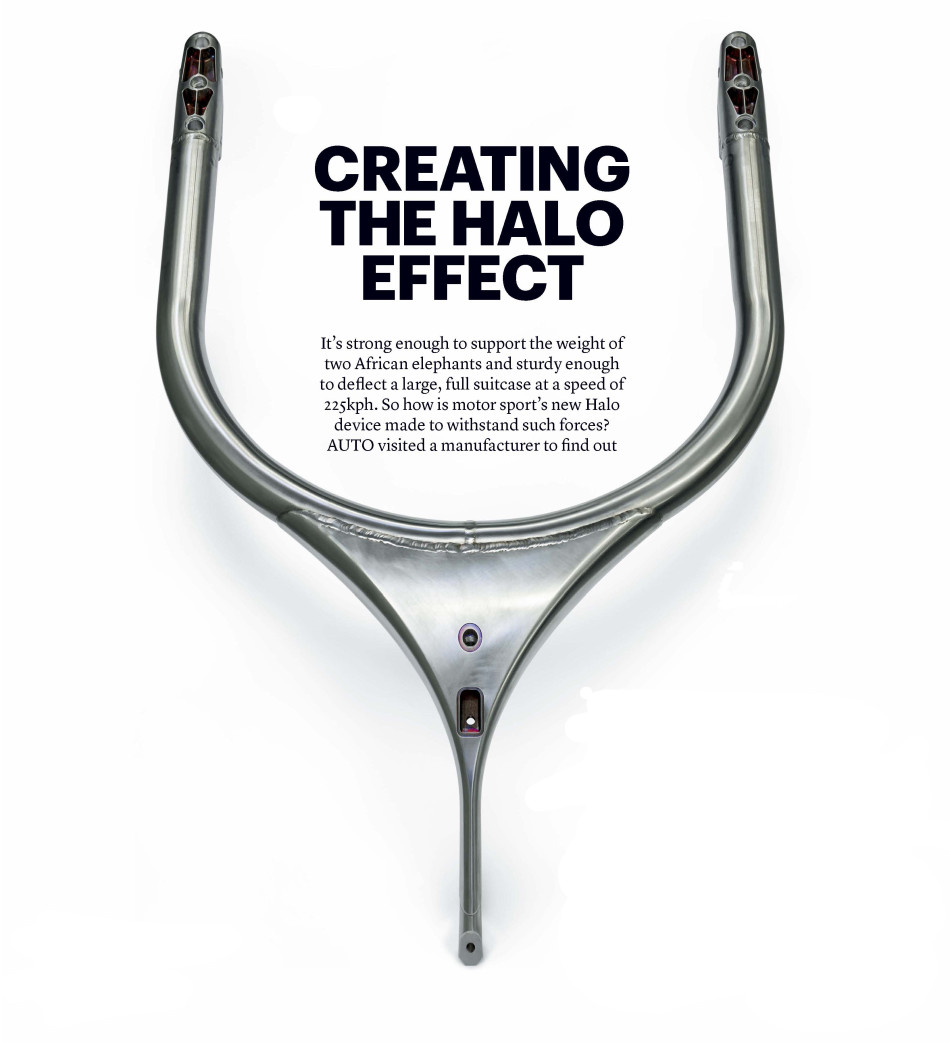
It all starts with titanium. Lots of titanium.
“We had to buy about 10 tonnes of high-strength titanium within one-and-a-half months, and receive it all in time and in perfect quality,” says Steffen Zacharias of Germany’s CP Autosport, one of the three manufacturers chosen by the FIA as official suppliers of the new Halo safety device.
The device is made from Grade 5 titanium, which is extensively used in the aerospace industry and is known for its high strength and stiffness compared to its relatively low weight. Fortunately, CP Autosport is well-versed in dealing with the stuff.
“We have a long history in motor sport, being involved since the 1990s, but we have an even longer background in aerospace materials and fabrication,” says Zacharias.
This experience put CP in pole position when it came to producing the first Halo prototype for FIA testing. Alongside the UK’s SSTT and Italy’s V System, CP was tasked with building a prototype within six-and-a-half weeks to be tested at the Cranfield Technical Centre, in the UK, in October 2017.
It was the first company to pass the test and has been chosen by nine of the 10 F1 teams to supply Halos this season (although some teams have purchased the device from all three companies).
It helps that CP’s manufacturing facility was ideally matched for the task.
“You need state-of-the-art machining parts to do the pre-machining and the post-welding final machining,” explains Zacharias. “You need a welding chamber in a closed atmosphere to do the welding process, and you need the supply chain for the material.”
Before working with the titanium it must be heat-treated to be optimised for the task. The company generally receives forged blocks that have been pre-treated to an individual CP specification to help withstand the loads that the final device will face.
The next step is to pre-machine and gun-drill the tubes that will be welded together. The Halo itself is built from five different parts. The half ring at the top is made from two quarters of the circle. Then there are the two end pieces that attach to the back of the car and the centre pillar in front of the driver.
The welding process is performed in a closed chamber to prevent any foreign objects from interfering with the material. The whole device then undergoes further heat treatment for additional strengthening before it is sent for testing.
Only the reference production device is tested to destruction at Cranfield. Each subsequent device is made from an exact process sheet that is approved by the Global Institute for Motor Sport Safety, the FIA’s safety research partner. But every device is geometry-checked, weight-checked and undergoes non-destructive testing, including x-rays and crack tests.
“We do these tests in-house,” says Zacharias. “Coming from the aerospace industry, we have a very intense testing area, including physical test benches and life-cycle testing. We test all our parts in-house by certified people to an aerospace standard.”
Once complete, the Halo is manually shot-cleaned to create an abrasive surface that makes it easier for teams to attach any aerodynamic parts that are permitted by the FIA.
All of these steps are essential for producing such a high-performance device. The Halo has to withstand 125 kiloNewtons of force (equivalent to 12 tonnes in weight) from above for five seconds without a failure to any part of the survival cell or the mountings. It must also withstand forces of 125 kN from the side. Without question, it is now the strongest element on a Formula One car.
“It has been a task to bring all the production technology together in a part like that,” says Zacharias.
But it helped that the F1 teams were fully supportive at every step of the way.
“I’ve been in this business now for almost 20 years and I have never experienced such an open-door philosophy from the teams,” admits Zacharias. “Whatever question we had, whichever expert we needed to talk to, we have been connected. Every door has been opened.”
CP has already produced and shipped 70 Halos and is expecting to have made 100 by the end of March. Not only is it supplying nine of the 10 F1 teams, it is also supplying the F2 and Formula E championships, which are then distributing to their teams.
So when the F1 teams line up on the grid for the first race of the season it will be a proud moment for the company.
“We have 200 people working here and we usually produce parts that are underneath the car and covered up by carbon fibre,” says Zacharias. “So to be able to show a physical part that’s more visible to the public means our employees can say, ‘this is what we’ve been working on’. So yeah, that really makes us proud.”